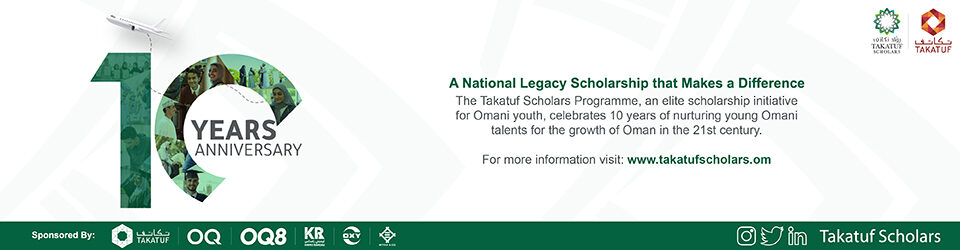
- Chile | 20 March 2022
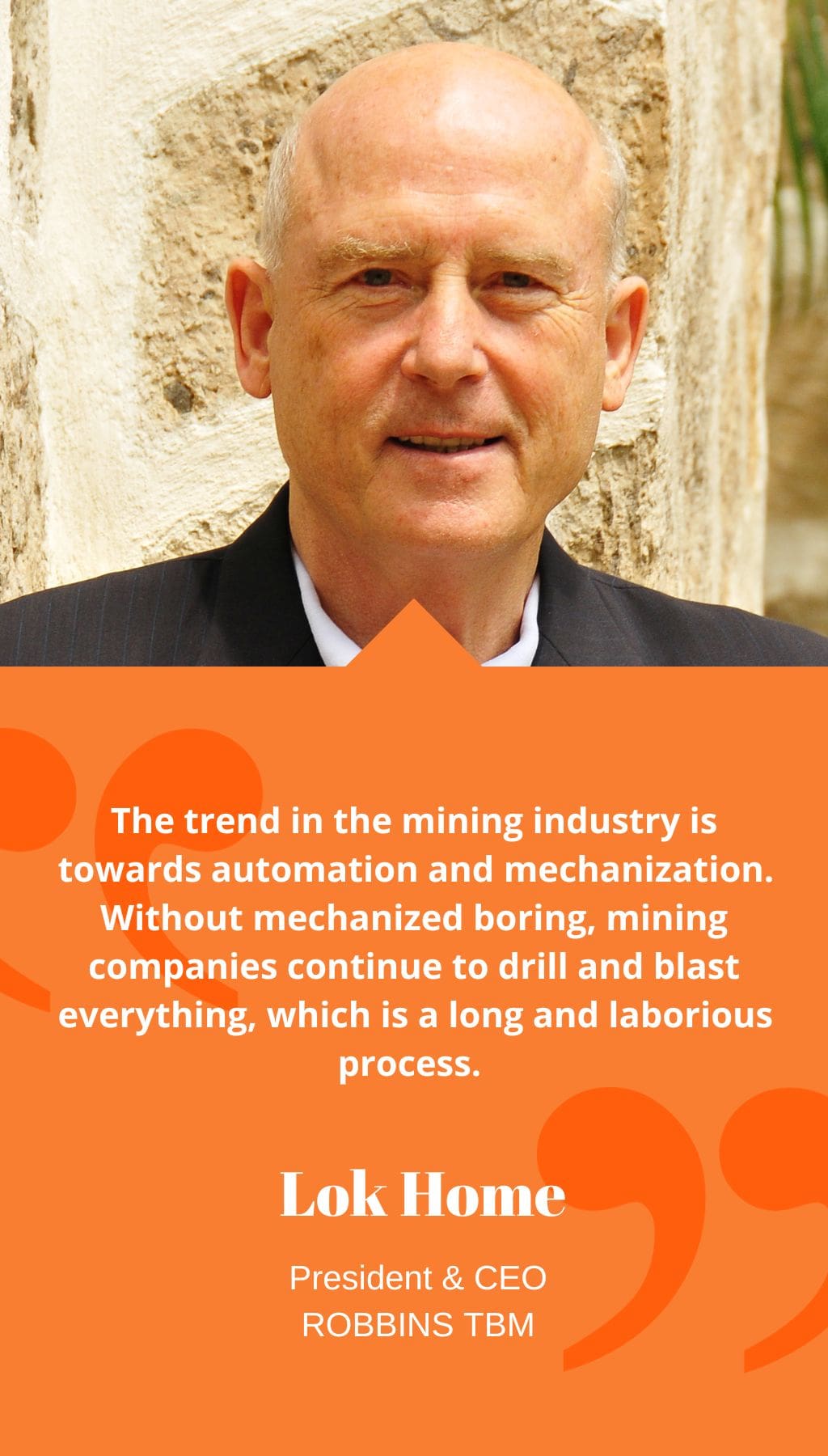
Could you explain how Robbins’ Mine Development Machine (MDM) 5000 underground mechanical excavation equipment works?
The MDM 5000 is designed specifically for mining applications as a mechanical excavation machine similar to a TBM. However, historically, 99% of TBMs have produced round tunnels, which is not an ideal shape in the mining industry as miners use vehicles to extract ore. Robbins’ goal was to provide miners with access tunnels using mechanical boring means, but with a flat floor and good ground support. Therefore, we developed the MDM 5000, which is essentially a TBM designed to achieve a flat floor, allowing for faster tunnel construction than what can be achieved with mechanical drill and blast.
What trends have you observed as mines transition to underground operations?
The trend in the mining industry is towards automation and mechanization. Without mechanized boring, mining companies continue to drill and blast everything, which is a long and laborious process. Mining companies are starting to realize that the only way to achieve mechanized mining underground is to accept mechanical excavation. We are already seeing an increase in demand for this technology from the industry, and we anticipate that in the next ten years, we will be mechanically excavating ore bodies. Environmental consciousness is also driving the trend towards underground mining and mechanical excavation, as nobody wants to see large open pits and piles of tailings.
Could you discuss some of the standout mining projects that Robbins has been involved in?
In the early days of Robbins, we used massive raise boring machines in several mines. More recently, the company worked with Stillwater Mining in Montana, where we used four round TBM machines for advanced exploration. About six years ago, we completed an incline for a coal mine in Queensland, where we started from the surface, bored down to the coal seam, extracted the TBM from the first heading, and then moved it over into another heading. This was a highly successful project where we utilized our civil engineering and mixed ground experience to move quickly from surface to the ore body.
Can you tell us about Robbins’ involvement at the Los Condores Hydroelectric Power Project in Chile?
The project did not go entirely as planned due to unforeseen geological difficulties encountered when we brought in the machines to bore the tunnels. However, Robbins, Enel, and the contractor worked well together to overcome these difficulties, and the two machines we supplied worked well.
Robbins also worked on the Olmos Trans-Andean Tunnel. What are some of the main challenges when tunneling in the Andean region?
Tunneling in high mountainous regions presents significant challenges due to the high cover above the tunnel. As the depth increases, rock stress changes, and this can lead to rock bursting, and groundwater can also be a challenge. We faced some challenging rock burst conditions during the Olmos tunnel project, but we were able to overcome them successfully. Today, we are equipped to handle any conditions, including high stresses, heat, and water inflows.
What type of partnerships is Robbins looking for with mining companies and contractors?
We are not just equipment suppliers; we want to take on a partner role with mining companies and contractors. We understand that the mining contractors are accustomed to drill and blast methods, and therefore, we want to bring our expertise in mechanical excavation to refine their expertise and ensure success. Collaborating with mining companies and contractors to develop innovative solutions that are not yet in the marketplace is critical for Robbins.