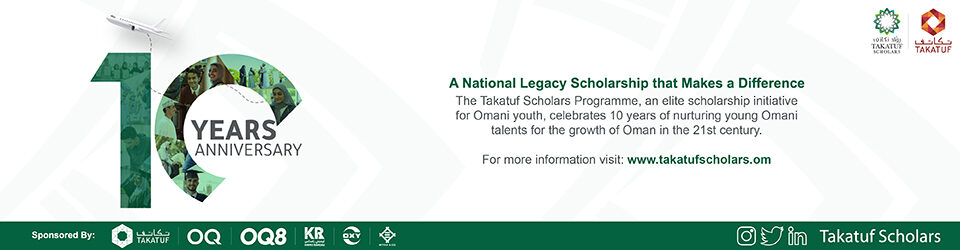
- France | 18 June 2018
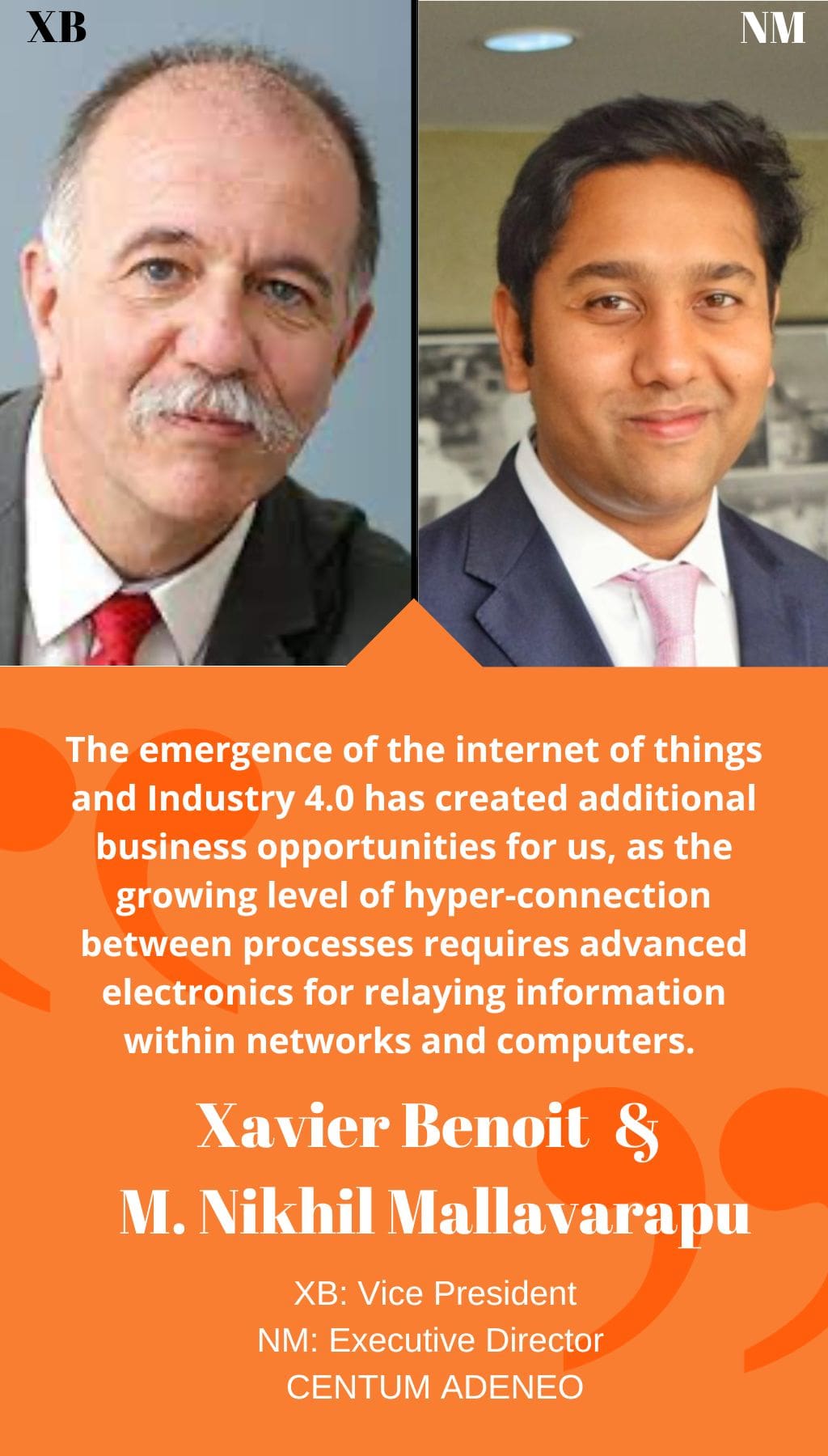
Can you provide us with an overview of Centum Adeneo and its contributions to the aerospace industry, both in Auvergne-Rhône-Alpes region and on a global scale?
Centum Adeneo, established in 1990 in Lyon and now a part of Centum Group based in Bangalore, has rapidly grown into a diverse electronics company with operations spanning North America, EMEA, and Asia. We specialize in various forms of electronics, ranging from digital electronics to power conversion storage, and offer a wide range of products for multiple sectors, including actuators, embedded computers, energy converters and storage equipment, and innovative services. We also develop the software for our electronics. Aerospace represents a significant portion, approximately 45%, of our global turnover.
What are the current areas of focus for research and development (R&D) at Centum Adeneo?
At Centum Adeneo, we are currently working on an R&D roadmap aimed at enhancing our expertise and providing increased value to our customers. Our main areas of focus include electronics system architecture, particularly safety architecture and design methodology, power supply, converters topology and regulation, miniaturization, and lightweight technologies. For instance, we are actively involved in a European-funded R&D project called “green taxiing,” which aims to develop methods to recover wasted energy during aircraft queuing on runways using specific storage technology that is already utilized in railway applications. Through such projects, we strive to stay at the forefront of innovative developments by applying technologies from other industries to the commercial aerospace sector, making us leaders in industry cross-fertilization.
Have there been any recent case studies that demonstrate significant benefits for your customers through customized solutions?
Yes, indeed. We have recently collaborated with Ratier-Figeac to create an electrical Trimmable Horizontal Stabilization Actuator, which is expected to be one of the first fully electric actuators, thanks to its fallback mode. In this project, we have designed all the equipment, including the controller architecture (safety level DAL B), the power board (4KW peak), the communication interface µAFDX and wireless communication for health monitoring, the software pack, and the box. While we are bound by non-disclosure agreements that prevent us from discussing many of our recent examples, in general, we are actively involved in developing actuators for landing gear and wings of more electric airplanes, as well as embedded power management.
How do you anticipate the growth of the global aerospace industry impacting the demand for services in the Auvergne-Rhône-Alpes region?
We have observed a growing trend of selling design and “Build to Spec” services, including feasibility, after-market support, prototyping, qualification, and manufacturing, to customers who have not traditionally incorporated electronic parts in their products, but are now driven to do so due to the increasing adoption of electronic processes within aircraft systems and interfaces in the aerospace industry. As a result, our business has been growing significantly, and we recognize the potential of this expanding customer base. We have developed expertise in working with such customers, introducing them to more electrical processes and assisting them in developing their own operations in this regard. Furthermore, the emergence of the internet of things and Industry 4.0 has created additional business opportunities for us, as the growing level of hyper-connection between processes requires advanced electronics for relaying information within networks and computers. We are actively working on developments in this field, including safety issues, where we possess considerable expertise. We are committed to providing efficient security support to our customers as they incorporate more electronics into their products.