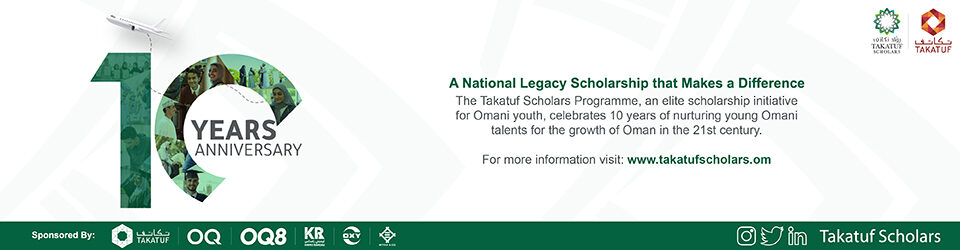
- Peru | 14 October 2021

How has Resemin performed in the last year?
2020 was a very bad year for many mining suppliers and manufacturers, including Resemin. Our recovery began in July, but we still ended the year with a net loss for the second time in my 32 years of business life. On the contrary, 2021 has been the best year in Resemin’s entire history, in which we have practically doubled our sales and sold 122 machines. However, a challenge we had to face was the supply chain crisis, which did not allow us to manufacture or sell everything we wanted.
What Resemin equipment aroused the most interest in 2021?
Among our underground mining drilling equipment, the best-selling models have been, firstly, roof bolters. We have supplied around 49 units globally. Resemin has the best roof bolter on the market in terms of reliability, productivity, ease of operation, maintenance cost, and minimal use of electronic sensors, and the market has realized this. The second best-selling model has been the MUKI family of equipment, which are mini jumbos for narrow vein mining. We have sold about 30 units worldwide. This is a niche where we have been well established for some time.
Can you talk about the disruptive innovations that Resemin offers for underground mining?
Resemin is growing thanks to our disruptive machines, which represent innovation at the highest level of creativity. Our most impactful disruptive development has been the entire MUKI family, including the tunnel development MUKI, long hole drill MUKI, and MUKI roof bolter. This machine has led many areas of mining company engineering to conceive the exploitation and development of narrow vein mines differently, allowing, for example, to reduce the size of tunnel sections.
In second place are our T99 series roof bolters, which we launched three years ago and are the most reliable on the market. In third place are the long hole production equipment, from the smallest size called MUKI LHBP to the medium size called Raptor 55 2R. These machines are gradually consolidating in Peru and other Latin American countries. In fourth place, we have developed the narrowest explosive loaders on the market, with 1.30-1.50 m wide. Additionally, we have created the T-Pointer system to convert our tunnel development jumbos to scalers, and we are currently waiting for the patent for this system. Finally, the Dual Jumbo is our most disruptive machine. At the moment, we have only sold nine units, so it still has to prove its worth. However, I see a great future for this machine.
What advances have you made in your battery-powered machinery?
Although we thought we would offer battery-powered equipment last year, its introduction has been postponed to 2022. We will launch the first machine to the mine in February, and if everything goes according to plan, we will be able to offer battery-powered equipment starting in December. We will be testing a machine for a customer for a whole year.
What trends are you observing in the adoption of new technologies in underground mining in Peru?
Currently, mining companies want to increase the automation of machines, so that they can perform their functions autonomously, work remotely, or be monitored through digital systems, for example. However, automation involves depending on numerous electronic sensors, which are very vulnerable to the poor environment of underground mines. For example, it is difficult to have quality wifi inside the mine. Therefore, many of the solutions offered in the market to automate these machines inside the mine finally do not work.