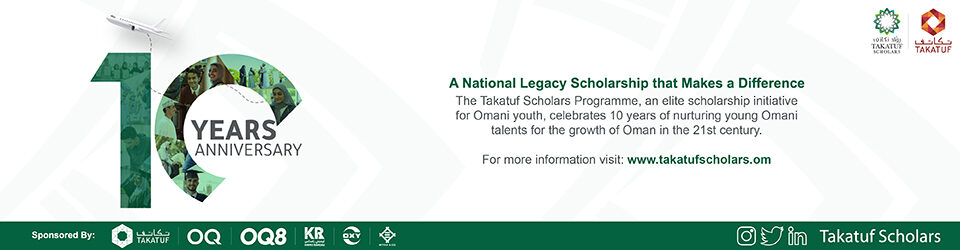
- Chile | 16 June 2022
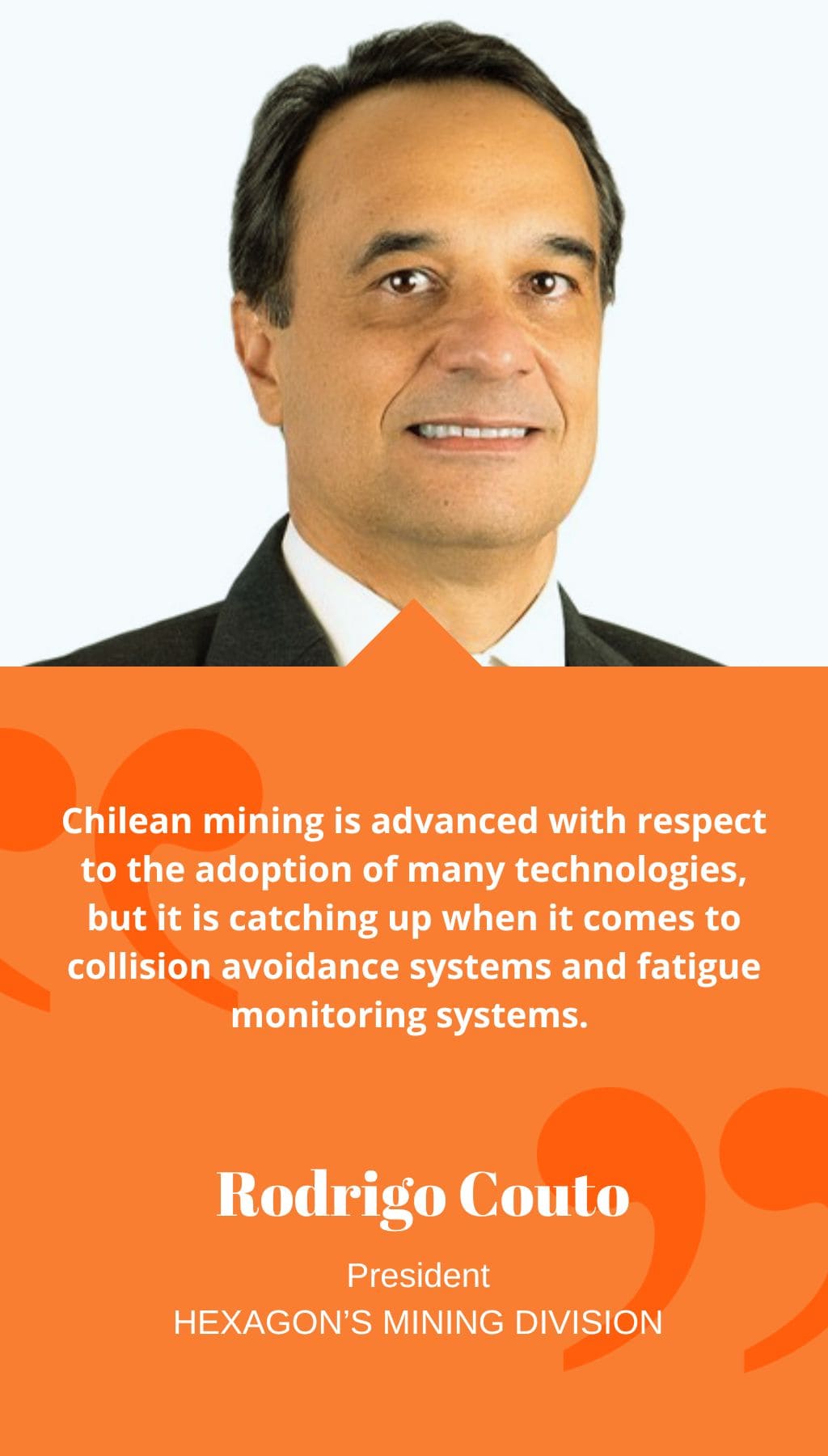
Can you discuss the evolution of Hexagon’s Mining division in recent years and what the company’s focus is today?
Hexagon’s Mining division has been scaling its mining technology portfolio over the past decade through a combination of organic growth, mergers and acquisitions, and partnerships. This includes the acquisition of Minnovare in January 2022, a leading provider of drilling technology that improves the speed, cost, and accuracy of underground drilling. Hexagon has also partnered with OEMs such as Liebherr to advance automation, or fellow technology companies such as HARD-LINE to expand teleoperation capabilities. Today, Hexagon’s mining division has a go-to-market strategy called ‘Power of One,’ which is a holistic solution connecting all processes of a mine from the pit to the plant, leveraging data from connected workflows to maximize productivity, safety, and sustainability at an operation. Hexagon’s technologies cover the areas of mine measurement, 3D modeling and design, and solve both surface and underground challenges with the goal of developing smart mines through a feedback loop between the real and digital worlds.
What are the main barriers to breaking down the silos that exist in the mining sector?
In 2021, Hexagon implemented 61 projects in Latin America, where the main challenge encountered was to break the paradigm of keeping data inside each silo. Clients care a lot about data and spend a lot of time collecting it, but many do not know how to transform data into actionable information. Hexagon offers clients an integrated ecosystem that guarantees a single source of data, which is automatically transformed into actionable information, connecting different workflows to enhance efficiency and productivity. One of our focuses is educating the market to convince users that sharing data in a meaningful way is going to be beneficial to their operations.
Can you elaborate on Hexagon’s partnerships with HARD-LINE and Liebherr?
Hexagon has partnered with HARD-LINE, a leading supplier of automation, teleoperation, and remote-control technology for the mining industry, to combine our technologies so that mine workers can be removed from dangerous environments. We have already implemented a remote center at Vale in Brazil so they can remotely manage tailings dams from an office. These remote operations run 24/7 to evaluate any kind of displacement or potential risk of failures of the dams in real time. Hexagon has also partnered with Liebherr to deliver next-generation automation solutions. The most impactful aspect of this partnership is Hexagon’s autonomous mission management system, which orchestrates fleet and unmanned mine traffic movements throughout the mine for optimized haulage.
Which areas of mining technology adoption have room for growth in Chile?
Chilean mining is advanced with respect to the adoption of many technologies, but it is catching up when it comes to collision avoidance systems and fatigue monitoring systems. We have been talking with the unions in Chile to explain that these technologies are not meant to expose drivers but rather to protect them instead so that they can return home safely.
What are the main factors you believe will drive the growth of mining technology in the coming years?
Over the past two years, the highest demand in the mining technology space has been for collision avoidance systems, fatigue monitoring systems, vehicle intervention systems (VIS), teleoperations, and autonomy. Hexagon is currently very much focused on everything related to safety, as well as data science, including AI and big data. Investors are looking to put their money into safe, profitable, and responsible operations. Because ore grades are getting lower and ESG standards are becoming stricter, mining companies have to invest in disruptive and transformational technologies to optimize their operations so they can continue to attract investment.